In recent years, consecutive heatwaves, droughts, and floods have led to unstable climate conditions worldwide, posing challenges to the development of the livestock industry.
Farmers have no choice but to purchase expensive feeds, hay, and other grains to nourish their animals. This exacerbates an already strained food chain and may lead to inflation rates higher than the current levels.
We can never predict when natural disasters will strike, but there are some things we can control: employing hydroponic techniques and efficiently utilizing limited resources in hydroponic fodder farming.
The profitability of feed farming remains a topic of debate, primarily due to the substantial energy costs and capital expenditures involved.
An increasing number of companies in China, the United States, the Middle East, and other regions are now focusing on hydroponic feed systems.
Here, I will share a case study of an intelligent forage factory in Tumxuk City, Xinjiang, China.
Grass Fodder Always Green in All Seasons
A smart fodder factory stands in the industrial park of Yong’anba Street, Tumxuk City, Xinjiang’s Third Division.
The planting area of this forage factory covers approximately 6,000 square meters, utilizing a five-story vertical planting structure that significantly boosts planting efficiency per unit area.
It annually produces about 3,000 tons of fresh, high-quality, high-protein forage (with a protein content of 32.2%). In terms of protein yield, it is equivalent to the production of approximately 3,700 acres of grassland in China.
This factory uses a fully integrated plant model with smart seedlings, photobiology, environment, soil, vertical cultivation, robotic harvesting, and feed production systems.
Interestingly, the forage here thrives in a misty atmosphere, without requiring water or soil.
In the seedling area, workers are busily sowing seeds, and you can already see many seeds that were sown earlier breaking through their shells and sprouting. A small enclosure can nurture up to 80,000 forage seedlings at a time.
After 15 to 20 days of growth, these seedlings are ready for transplantation into the vertical ecological cultivation zone for fully automated nurturing.
The farmer customizes the nutrient absorption requirements for different types and growth stages of forage. They convert the necessary nutrients for the forage into a nano-mist form, precisely controlling various indicators such as water content and oxygen levels. This approach achieves a remarkable water-saving rate of 95%.
Entering the cultivation area, under the bright LED grow lighting, rows of flourishing forage on the five-tiered vertical planting racks catch your eye.
Inside the cultivation area, various sensors monitor real-time data, including temperature, humidity, light intensity, CO2 concentration, and more.
Through the glass wall of the cultivation area, you can see a large data-driven management platform covering the entire wall, serving as the brain of the smart forage factory. It’s continuously displaying real-time data for all aspects of the factory’s operations.
This platform is responsible for receiving and processing plant growth data uploaded by the vertical ecological cultivation system, digital soil system, photobiological system, crop environmental control system, and robot system.
It stores and provides real-time access to all the data generated within the forage factory.
Barley Fodder System Takes 7 Days to Harvest
Auxgrow’s team has also completed the construction of an indoor forage farm in the Aksu region of Xinjiang, China. We’ve integrated agricultural IoT for automated management, thereby achieving high efficiency and productivity.
From seed soaking to planting, the entire production process is automated. After soaking in the seed soaking area, the seeds are conveyed directly to the planting area via a conveyor belt.
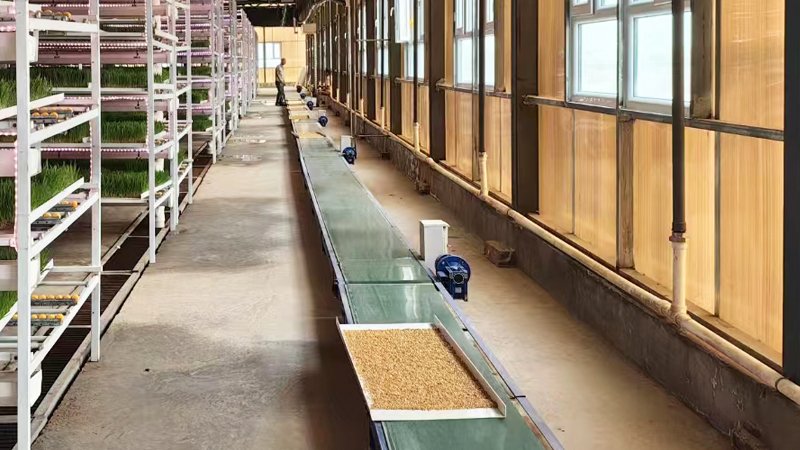
Each level of the planting cabinet is equipped with pulley devices, making the harvesting and planting process more efficient and convenient.
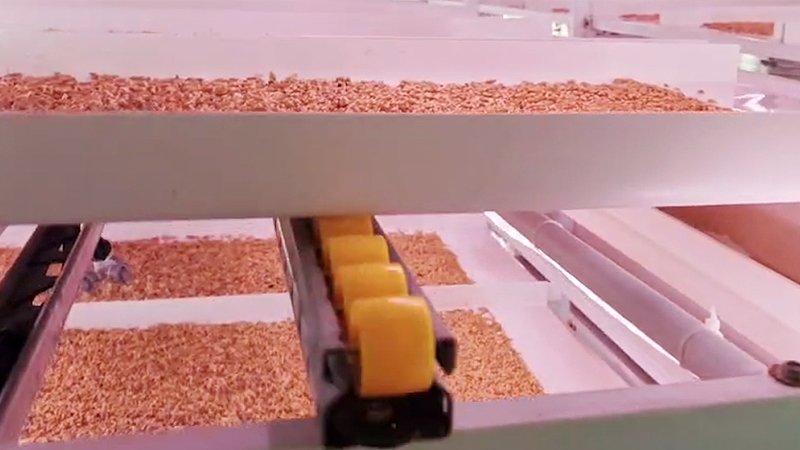
The single-sided open design, with a drainage channel at the bottom, ensures effective drainage, preventing any potential rotting of seeds or forage.
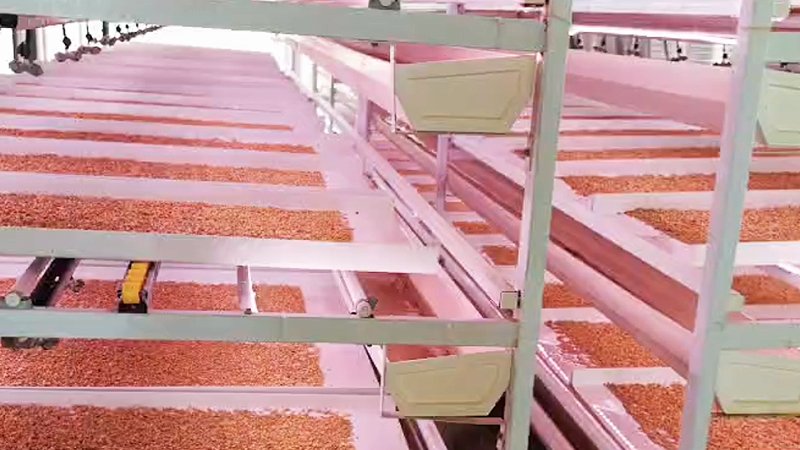
By utilizing an effective multi-tiered vertical planting method, the yield per unit area has doubled, effectively solving the issue of insufficient forage for livestock and poultry.
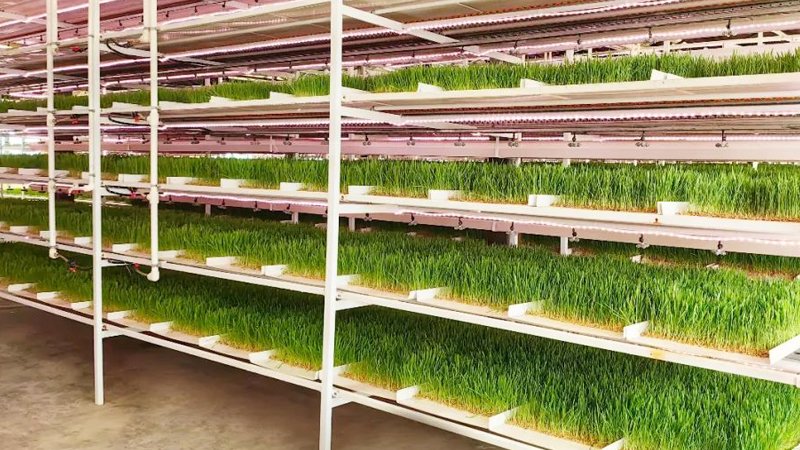
Multiple spray nozzles in each tier automatically irrigate to keep the forage consistently moist for healthy growth.
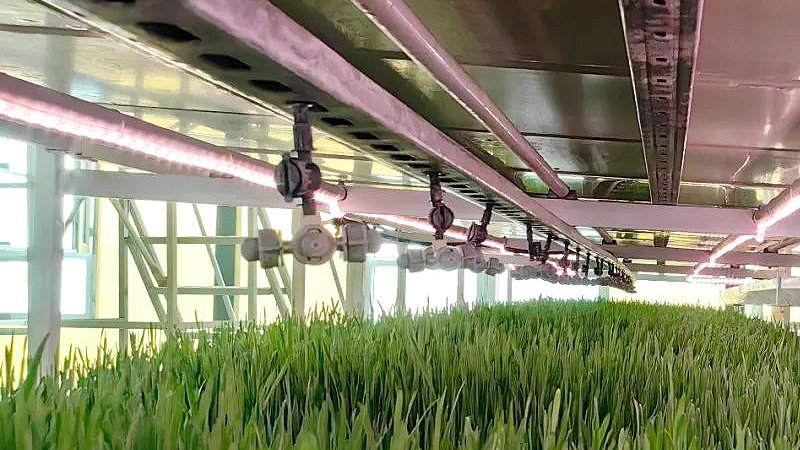
The lighting system for proper photosynthesis includes two sets of supplementary plant lights on each tier.
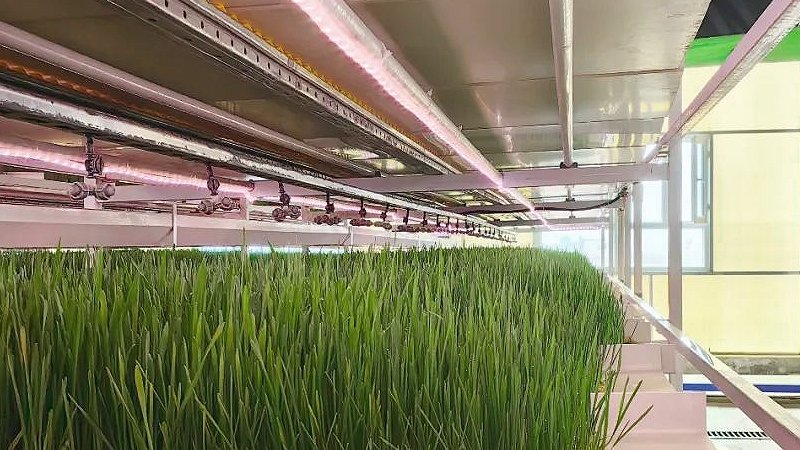
This vertical hydroponic system in a plant factory yields high-quality crops with a shorter growth cycle.
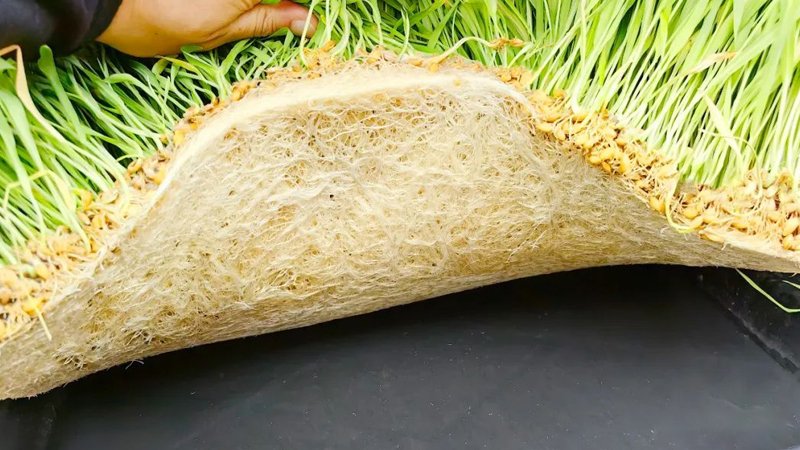
Entre em contato com a Auxgrow hoje mesmo
The construction of the smart forage factory represents a significant step toward the global transition from traditional agriculture to digital agriculture, optimizing the growth environment for forage to the highest degree.
Indeed, you can determine the construction model of the forage plant factory based on your specific circumstances.
- If you have enough space, you can set up a large greenhouse.
- Even with limited space, a flexible container plant factory can yield substantial crops.
If you would like to learn more about hydroponic fodder farming, please do not hesitate to get in touch with us. We would be happy to provide you with additional information and further examples to showcase its benefits.
Jayes
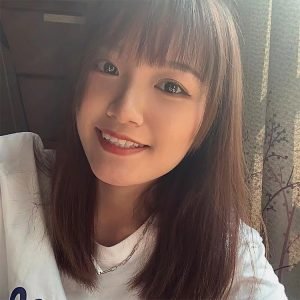
Como gerente de marketing digital da AUXGROW, Jayes combina paixão por sistemas hidropônicos e experiência em luzes LED de cultivo. Com experiência prática e profundo conhecimento, Jayes guia você pelo mundo do cultivo sustentável.