Efnisyfirlit
We must recognize that, as of now, the energy consumption of a plant factory is relatively high, since the vast majority of the facilities and equipment are powered by electricity.
Precisely because of the high energy use, there’s a lot of debate surrounding this technology.
However, we believe that the true value of plant factories cannot be determined solely by their energy usage. Rather, their importance lies in their ability to tackle the difficulties of cultivating crops in unfavorable weather conditions and environments.
It is extremely difficult to grow crops outside in regions with extreme temperatures or in areas with problematic soil and geology conditions. It is precisely because of the technology of plant factories that we can produce crops in these extreme conditions.
Therefore, plant factories are worth the time and effort for younger generations and modern farmers to explore and research. It’s a profoundly meaningful agricultural field.
In this article, we delve into the fascinating world of plant factories.
Plant Factory Meaning
Before understanding plant factories, it is necessary to clarify their implications and extensions for facility agriculture and vertical farming.
Facility agriculture is a typical modern agricultural production method.
People carry out agricultural production inside these facilities by comprehensively applying engineering equipment, environmental technology, and biological techniques, to optimal environments needed for plant and animal growth and development.
A typical form of facility agriculture is the plastic greenhouse, while the evolved version is vertical farming. The latest representative of vertical farming is the plant factory.
The essence of a plant factory is to streamline agricultural production. Under fully industrialized conditions, crops are grown industrially, completely eliminating the characteristic of agriculture relying on the weather.
The basic model of a plant factory involves high-precision automatic control of environmental conditions for plant growth, such as water, fertilizer, air, light, and temperature, through computers, electronic sensing systems, and agricultural facilities, providing the most suitable growth conditions for plants.
The planting method in a hydroponic plant factory is to carry out multi-layer cultivation through vertically stacked growth racks. This dramatically increases land utilization, thus circumventing the issue of insufficient arable land.
The industrial chain of a plant factory is mainly composed of three parts: upstream agricultural technology component manufacturers, midstream plant factory enterprises and solution providers, and downstream agricultural product channel sales.
How do Plant Factories Work?
Plant factories, vertical farming, and indoor planting all belong to the advanced stage of facility agriculture, which is intelligent facility agriculture. It can also be commonly understood as a more refined, smarter indoor plant factory greenhouse.
Let’s see how they work!
Firstly, the growing environment is completely controlled. That means setting the right temperature, humidity, light intensity, and even CO2 levels to ensure plants grow as best they can.
Because everything is indoors, you don’t have to worry about weather or pests, which can be a real problem with traditional farming.
Although there are different methods of soilless cultivation, a universal standardized system has not yet been established.
Plant factories often use hydroponics or aeroponics. Instead of soil, plants dangle their roots in nutrient-rich water (hydroponics) or they get sprayed with a nutrient mist (aeroponics).
This method can use far less water than traditional farming.
Lighting is key. Sunlight isn’t an option indoors, so instead, LED lights are used. These lights are designed to emit only the wavelengths of light that plants need most for photosynthesis, making them highly efficient.
Lastly, automation is a big part of these factories. Machines take care of planting, harvesting, and sometimes even packaging. This can cut down on labor costs and increase efficiency.
Advantages of Plant Factory
In simple terms, plant factories have special advantages in terms of cultivation conditions, nature-friendliness, and intelligence.
Surpassing Land
With the continuous expansion of cities, the development demand for high-value-added industries, and the advancement of environmental protection movements, the tension of agricultural land use has been further intensified.
One of the major potentials of plant factories lies in changing the scarcity of land.
Through multi-layered vertical cultivation, the unit area yield of a plant factory and the utilization of land and space resources far exceed traditional planting modes.
Some plant factories that adopt a vertical planting model can reach 10-14 layers, and under the same occupied area, the actual effective area can increase by 4.2 times.
With the advancement of technology and the improvement of internal environment regulation capabilities, there is still considerable room for improvement in this figure.
If you are interested in this, please click to learn about Auxgrow’s vertical hydroponic system.
The widespread use of soilless cultivation modes such as hydroponics, sponge substrate, and aeroponics has essentially freed plant factories from the traditional facility agriculture’s dependence on the soil.
This freedom allows for almost complete flexibility in site selection. Abandoned factories, buildings, and containers can all be converted into plant factories.
In regions with a relative scarcity of water resources, like sandy and saline-alkali lands where traditional agricultural production is extremely difficult, the operation of plant factories is not affected.
Stutt yfirlit
The freedom of location selection brings a business model to plant factories that differs from traditional agriculture. That is, to carry out large-scale planting in the suburbs or even within the city, bringing the place of production as close as possible to the consumers’ tables.
This helps reduce dependence on long-distance transportation and multi-level distribution, lowering storage and transportation costs while supplying fresher agricultural products.
The wide range of location conditions combined with high space utilization also makes plant factories the best, or even the only choice, in scenarios where space is scarce, such as islands, polar regions, space stations, and even future lunar research stations.
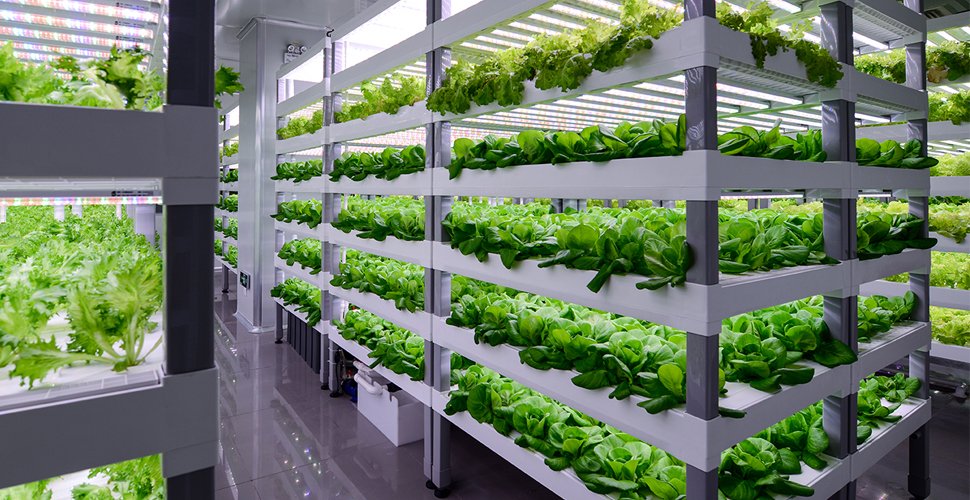
Beyond Nature
In addition to relying on cultivable land, traditional agriculture also depends on a series of natural conditions such as temperature, season, precipitation, and sunlight.
Greenhouse planting can somewhat reduce dependence on the external environment, achieving off-season and year-round production. But the vision of plant factories is even more ambitious.
An ideal plant factory does not rely on natural light at all but instead uses artificial light sources to meet the growth needs of plants. The industry currently mainly uses LED plant lights.
The efficiency of LED grow lights lies not in simply imitating natural light, but in adjusting the light intensity, quality, and cycle according to the biological effects of the crops being grown, thereby more effectively promoting plant growth.
By supplementing with grow lights or using LED plant lighting throughout the process to irradiate plants, plant growth can be promoted, yield can be increased, product shape and color can be improved, and pest diseases can also be reduced.
The control precision of the internal environment in a plant factory far exceeds that of traditional facility agriculture, making year-round production possible.
All internal growth elements are maintained as much as possible under the optimal growth parameters of the crops so that the crops are no longer affected by seasons, natural disasters, and climate.
Because it achieves quasi-isolation from the outside world, the intrusion of pests and diseases is minimized as much as possible. The growing environment inside the factory is cleaner, and the health of the plants is better.
Stutt yfirlit
To summarize, plant factories aim to increase their yields, have greater control over growth cycles, ensure more consistent growth, and achieve stable and predictable yields.
Reports suggest that tomatoes in a plant factory can be harvested just two months after planting, compared to a hundred-day growth cycle for traditional greenhouse tomatoes. Leafy vegetables can be harvested in just 1/5 to 1/3 of the time required for outdoor cultivation, with no need for fallow periods.
For example, AeroFarms, touted as the world’s largest vertical farm, can harvest vegetables every 16 days, with an annual total yield of about 900,000 kilograms.
The Chinese Academy of Agricultural Sciences research results have successfully achieved a rice harvest in about 60 days in a plant factory. This has effectively halved the traditional growth cycle of about 120 days for rice cultivation in open-field environments.
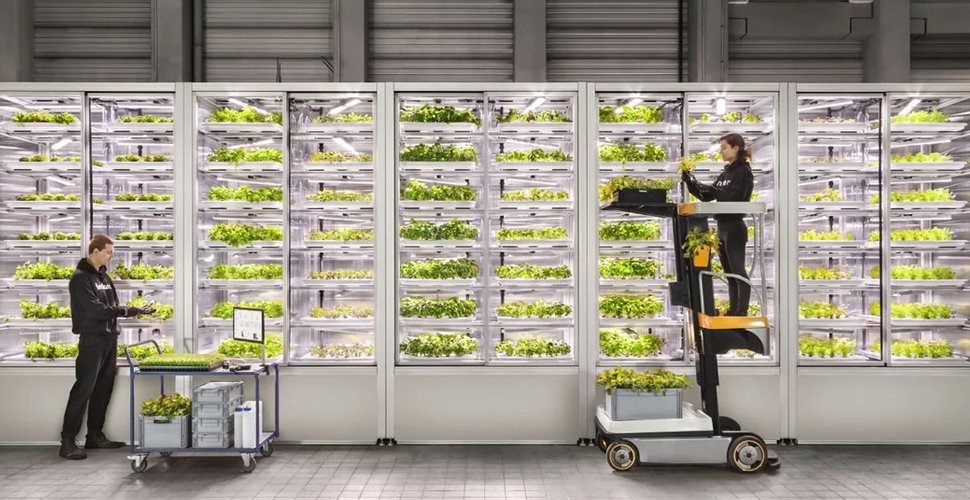
Green Industry
Although modern agriculture cultivates many different plants, it, unfortunately, does not prioritize environmental protection.
The act of cultivating land does not inherently produce natural pollutants. However, farmers often depend on large amounts of fertilizers and pesticides while planting to ensure good crop yields.
The excessive use of fertilizers and pesticides is not environmentally friendly. It could lead to soil degradation, groundwater pollution, and residues that are unsafe for the human body.
According to related reports by the United Nations, 13% to 21% of global greenhouse gas emissions are related to the agricultural sector. Tackling the climate crisis also requires initiatives from agriculture.
Plant factories, tending to be located close to consumers’ tables, can shorten transport distances, thus helping to alleviate carbon emissions to a certain extent.
At the same time, agriculture inevitably involves a lot of water usage.
According to the United Nations Food and Agriculture Organization’s “The State of Food and Agriculture 2020” report, agricultural water use accounts for 70% of the global consumption of water resources.
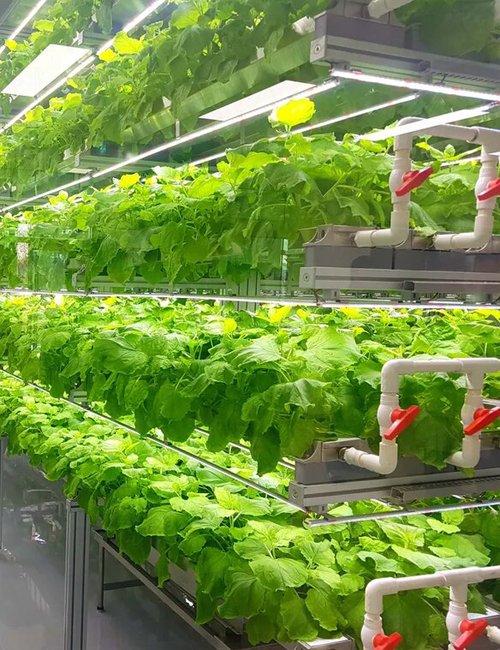
Water
Thanks to the relatively closed and highly controllable environment, plant factories can achieve a very high level of water resource recycling.
The production capacity of Auxgrow’s hydroponic vertical system is greatly improved, and its water consumption is only about 5% of that of traditional cultivation methods.
The scientifically designed smart irrigation system can determine the precise water balance required by the crop. Coupled with the recycling system, it can reduce water consumption by 90% to 97%.
Fertilizer
The existence of intelligent systems also strengthens the utilization rate of nutrient solutions in plant factories.
The fertilizer utilization rate in plant factories can reach 2 to 3 times that of open-field cultivation.
Systems such as aeroponics and integrated water and fertilizer can ensure that nutrients are delivered directly to the root system. Nutrients that are not absorbed can also be recycled, thereby reducing the excessive use of fertilizers.
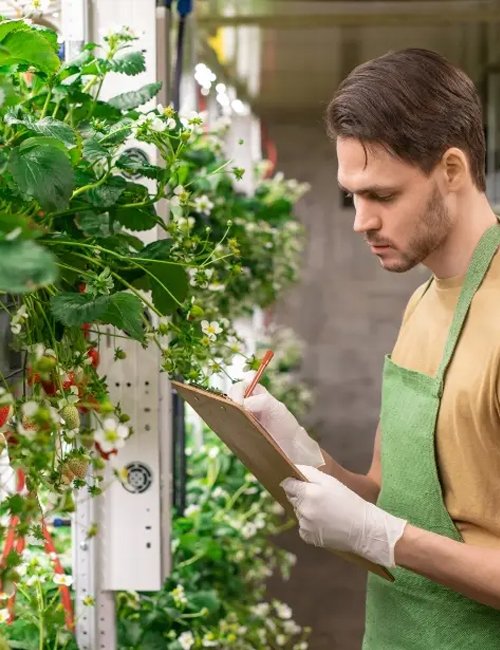
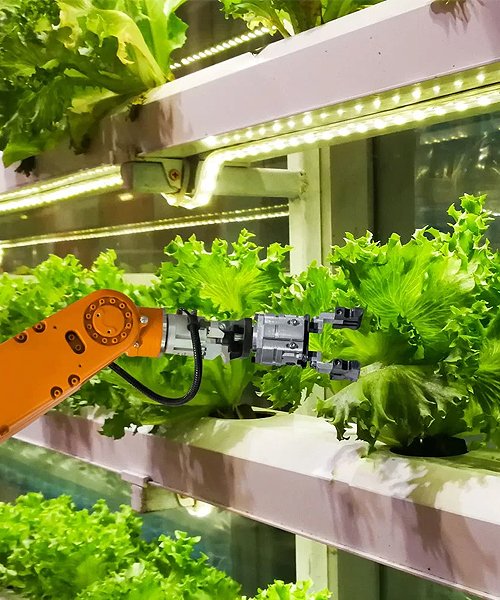
Automation
Plant factories come equipped with a plethora of intelligent facilities, making highly automated robot operations a viable model.
Automated robots can relocate plants and manage their density. This can minimize human errors and address the issue of labor intensity in agricultural production.
Undoubtedly, implementing this measure is a wise decision considering the continual increase in labor costs and inadequate agricultural compensation.
Pesticides
Crops like chili peppers, eggplants, tomatoes, cucumbers, and melons have crop rotation issues.
Although many plant factories avoid these issues by not relying on natural soil and growing high-profit crops that are not affected by continuous cropping, they still face their unique challenges.
However, most plant factories do not have these problems, they do not need natural soil, and high-profit crops do not have to worry about yield reduction due to intensive continuous cropping.
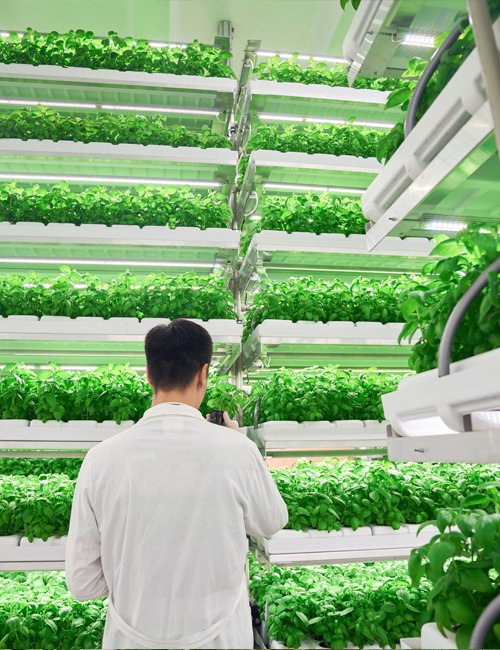
Disadvantages of Plant Factory
The various benefits offered by plant factories are attracting attention and investment from several sectors.
However, similar to any emerging technology, plant factories face various challenges on the road ahead.
These challenges pose significant questions for investors and innovators, offering an area for exploration and improvement. Here, we examine some of the key challenges that plant factories face.
High Costs
Apart from the substantial funding requirements for start-ups, the day-to-day operations of plant factories can be quite expensive.
Plant factories replace natural conditions with artificial environments, and the cost is far greater energy consumption than traditional agriculture.
Currently, there is no unified design scheme for plant factories, and the facilities of different companies vary. However, energy is without exception the most significant cost component.
Click to check how much electricity the LED plant light consumes, which will be beneficial for the implementation of your initial planning blueprint.
As well as you need to know the daily light requirements of your target crop, making good timing adjustments will be good for your wallet!
Crop Limitations
Plant factories are not suitable for growing all crops, such as field crops like wheat, rice, corn, cotton, and soybeans. For now, most plant factories utilize hydroponic, aeroponic, and soilless cultivation modes, which are only suitable for crops with shallow root systems.
Expanding the range of crops that can be economically grown in these systems is a significant challenge.
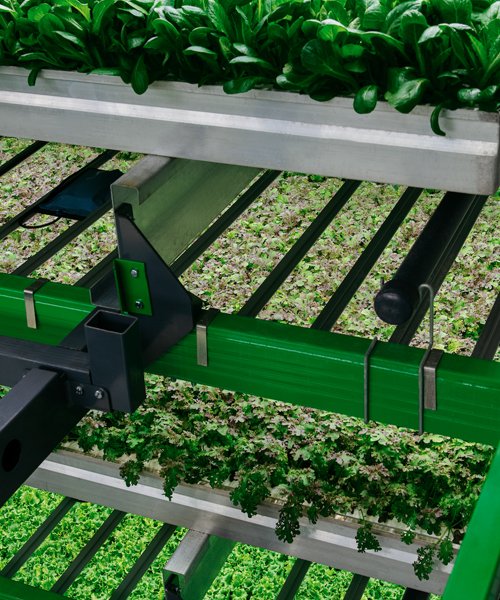
Low Market Acceptance
Although plant factories can produce high-quality crops, their acceptance in the market is not guaranteed.
Some people are skeptical about hydroponic vegetables, mainly because they lack understanding or have misconceptions about the hydroponic growing process.
If feasible, organizing seminars, talks, or farm tours can help people understand the science behind hydroponics and dispel misunderstandings.
Holding tasting events at farmers’ markets, stores, or public events can help consumers get up close with hydroponic vegetables. Educational activities can help change consumer perceptions of green factory plants.
However, these challenges also present opportunities for innovation and growth. Making the sector an exciting space for investors and entrepreneurs who rise to the challenge.
Success Stories of Plant Factories
Absolutely, successful case studies in the realm of plant factories provide valuable insights.
These success stories illustrate that despite the challenges, with innovative technology and business models, plant factories can indeed be viable, sustainable, and profitable.
Plenty (USA). Plenty uses state-of-the-art technology to grow a variety of crops, including leafy greens, in their vertical farms. Their success comes from their commitment to taste, texture, and sustainability.
Urban Crop Solutions (Belgium). Their innovative solutions for indoor vertical farming and commitment to sustainability have attracted eco-conscious consumers.
Vertical Field (Israel). Their commitment to growing a variety of crops sustainably in vertical farms has resonated with consumers interested in eco-friendly practices.
Mirai (Japan). Mirai’s focus on growing pesticide-free produce indoors has been a hit among consumers who want clean, safe food.
Sky Greens (Singapore). By providing fresh produce in densely populated Singapore, they’ve tapped into the demand for local and fresh food.
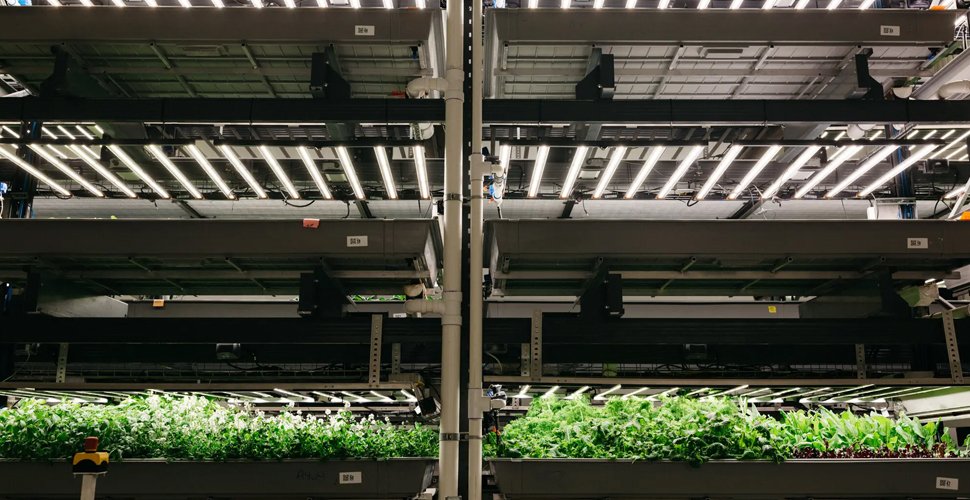
Future of The Plant Factory
Current plant factories are not highly industrialized, and the high energy costs associated with plant factories or vertical farming are indeed a major barrier to growth and scalability.
There are two most common ideas to address the problem of high energy costs.
Improving Energy Efficiency
Improving the light-electricity conversion efficiency is a current focus in plant factories.
By choosing energy-efficient and effective equipment, and designing precise internal environmental control systems, one can make the most of energy usage.
LED plant lights are a choice under this concept. Similarly, improvements in insulation and HVAC (Heating, Ventilation, and Air Conditioning) technology can reduce the energy needed for temperature and humidity control.
Integrating Renewable Energy Sources
Building plant factories adjacent to photovoltaic, wind, and hydroelectric power plants can provide access to cheaper energy. However, this approach has its limitations: power generation facilities are usually located a certain distance from consumer markets.
This can lead back to the traditional long-distance transport model, potentially weakening the economic viability of the plant factories. While it may be challenging for plant factories to compete with large-scale farming, it doesn’t mean that they have no appeal to any country or region.
Focus on Enhancing Benefit
For instance, oil-producing countries on the Arabian Peninsula generally have harsh natural conditions, making outdoor farming quite challenging.
However, these countries are also exceptionally wealthy, with unusually cheap energy prices, and the imported vegetables that consumers eat daily are already expensive. For these unique market conditions, plant factories might be an excellent choice.
While some of these solutions require significant upfront investments, the long-term savings they offer can make plant factories more economically viable.
The key is to approach the problem from multiple angles, combining different technologies and strategies to maximize energy efficiency and minimize costs as much as possible.
If you’re looking for a tailored plant factory system, are interested in buying LED plant lights for your factory, or considering a mini-vertical system to assess its potential, please contact Auxgrow today.
Jayes
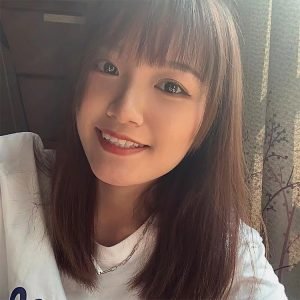
Sem stafrænn markaðsstjóri hjá AUXGROW sameinar Jayes ástríðu fyrir vatnsræktunarkerfum og sérfræðiþekkingu í LED vaxtarljósum. Með praktískri reynslu og djúpum skilningi leiðir Jayes þig í gegnum heim sjálfbærrar ræktunar.